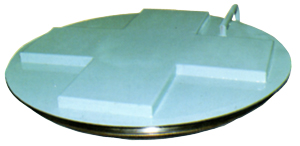
課題
得意先からの改善要求に、代替策を検討。解決策は見つけられるか・・・
電力機器の製造を行っているB社。工場や商業施設で使用される変圧器・変成器に豊富な実績を持っていた。
ある日、B社の得意先ユーザーから、変圧器に組み込まれているコンサベータに関して問い合わせが入った。具体的には「コンサベータに使われているゴム製隔膜の劣化について、改善を検討して欲しい」という内容であった。
B社では、構造が簡単でコストが安価なゴム製隔膜で制御するコンサベータを自社で製作し、電力機器に組み込み、納入していた。しかし、屋外や温度差が激しい場所で利用される大型機種の場合、ゴム製隔膜がダメージを受けやすく、劣化の進行を早めてしまうのだ。
この他にも、「ゴム膜のメンテナンスの頻度を減らせないか」「油中への酸素、窒素飽和濃度を減らせないか」などといった要望があったことから、B社の開発チームは、ゴム膜の代替を早急に検討することにした。
解決策は2つに絞られた。しかし、どちらも実現できず・・・
検討を重ねた結果、ゴム製隔膜の替わりに金属隔膜を使用する方向で話が進んだが、その製作を今までどおり自社で行うか、外部の部品メーカーに製作してもらうかについては、どちらも未経験であることから、結論はすぐに出せなかった。
ひとまず、自社で金属隔膜を使ったコンサベータの試作を行うことにした。ところが、初めて扱う金属の動きや、温度変化に対応するための構造設計、特殊材を使用した溶接技術など多くの問題が一気にのしかかったため、試作を一旦中止した。
自社での製作に限界が見えたことから、対策を新たな部品メーカー探しに切り替えた。しかし、いざ探し始めると今まで取引のあったところは、どこも対応できず、気密性の高い部品を製作できる企業の情報は少ないことから、スタッフは頭を抱えるばかりであった。
課題のポイント
従来から採用していたコンサベータのゴム製隔膜について、得意先から改善要求が発生
自社で金属隔膜を使った製作を試みたが、設計や溶接がうまく行かず、断念
気密性の高い部品製作ができるメーカーを探すが、情報が少なく、見つけられない
解決のポイント
伸縮設計、金属溶接のスペシャリストが、金属ベローズを使用したオリジナル隔膜を設計、製作
材料の選定から組み上げまで、国内の専門工場で行ったものを納品
メンテナンスの工数が大幅に減少し、10%のコストダウンを実現
スペシャリストが国内で製作したコンサベータで、コストダウンも実現!
メーカー候補が見つからず、途方にくれていたB社の開発スタッフ。そんなとき、受変電設備で取引のある営業から、「入江工研なら気密溶接が得意で、材料選びから相談できるので、1度話しをしてみては」とのことで、担当者を紹介してもらった。
早速、入江工研の担当者はB社を訪問して、課題のヒアリングを行った。その上で入江工研の強みである気密溶接の精度の高さや、ベローズの材質・肉厚を利用環境に応じて自由に選べること、しかもこれらの製作工程をすべて国内の自社工場で対応していることを説明し、課題解決に向けて力になれることを伝えた。また提案に伴い、B社のコンサベータに最適な金属隔膜の試作も合わせて行うことにした。
3週間ほどで試作が出来上がり、B社の試験環境で検証を実施した。評価は、温度上昇による膨張をベローズが吸収して、溶接部に損傷を与えず、圧力を安定させ続けられるかという点と油中への酸素、窒素飽和濃度の改善という点で行い、現行のゴム製隔膜のものと比べることにした。
まず2つのコンサベータに、高温、冷却の負荷を何度も繰り返したところ、ゴム製隔膜に小さな亀裂が見え始めたが、入江工研製の金属ベローズを用いた方は、安定した動作を続けた。また、油中への酸素、窒素飽和濃度について調査したところ大幅な改善が見られ、油の耐久性向上についても実証された。
この結果を受け、B社は入江工研の採用を決定。過酷な環境下で使用するためのモデルとして、このコンサベータを組み合わせて納入したところ、電源装置を屋外に設置する事業者から高評価を得た。
また、劣化の心配がなくなっただけでなく、メンテナンスの頻度や、工数も大幅に抑えることができ、トータルで10%以上のコストダウンも手に入れることができた。
得意先からの改善要求に、代替策を検討。解決策は見つけられるか・・・
電力機器の製造を行っているB社。工場や商業施設で使用される変圧器・変成器に豊富な実績を持っていた。
ある日、B社の得意先ユーザーから、変圧器に組み込まれているコンサベータに関して問い合わせが入った。具体的には「コンサベータに使われているゴム製隔膜の劣化について、改善を検討して欲しい」という内容であった。
B社では、構造が簡単でコストが安価なゴム製隔膜で制御するコンサベータを自社で製作し、電力機器に組み込み、納入していた。しかし、屋外や温度差が激しい場所で利用される大型機種の場合、ゴム製隔膜がダメージを受けやすく、劣化の進行を早めてしまうのだ。
この他にも、「ゴム膜のメンテナンスの頻度を減らせないか」「油中への酸素、窒素飽和濃度を減らせないか」などといった要望があったことから、B社の開発チームは、ゴム膜の代替を早急に検討することにした。
解決策は2つに絞られた。しかし、どちらも実現できず・・・
検討を重ねた結果、ゴム製隔膜の替わりに金属隔膜を使用する方向で話が進んだが、その製作を今までどおり自社で行うか、外部の部品メーカーに製作してもらうかについては、どちらも未経験であることから、結論はすぐに出せなかった。
ひとまず、自社で金属隔膜を使ったコンサベータの試作を行うことにした。ところが、初めて扱う金属の動きや、温度変化に対応するための構造設計、特殊材を使用した溶接技術など多くの問題が一気にのしかかったため、試作を一旦中止した。
自社での製作に限界が見えたことから、対策を新たな部品メーカー探しに切り替えた。しかし、いざ探し始めると今まで取引のあったところは、どこも対応できず、気密性の高い部品を製作できる企業の情報は少ないことから、スタッフは頭を抱えるばかりであった。
課題のポイント
従来から採用していたコンサベータのゴム製隔膜について、得意先から改善要求が発生
自社で金属隔膜を使った製作を試みたが、設計や溶接がうまく行かず、断念
気密性の高い部品製作ができるメーカーを探すが、情報が少なく、見つけられない
解決のポイント
伸縮設計、金属溶接のスペシャリストが、金属ベローズを使用したオリジナル隔膜を設計、製作
材料の選定から組み上げまで、国内の専門工場で行ったものを納品
メンテナンスの工数が大幅に減少し、10%のコストダウンを実現
スペシャリストが国内で製作したコンサベータで、コストダウンも実現!
メーカー候補が見つからず、途方にくれていたB社の開発スタッフ。そんなとき、受変電設備で取引のある営業から、「入江工研なら気密溶接が得意で、材料選びから相談できるので、1度話しをしてみては」とのことで、担当者を紹介してもらった。
早速、入江工研の担当者はB社を訪問して、課題のヒアリングを行った。その上で入江工研の強みである気密溶接の精度の高さや、ベローズの材質・肉厚を利用環境に応じて自由に選べること、しかもこれらの製作工程をすべて国内の自社工場で対応していることを説明し、課題解決に向けて力になれることを伝えた。また提案に伴い、B社のコンサベータに最適な金属隔膜の試作も合わせて行うことにした。
3週間ほどで試作が出来上がり、B社の試験環境で検証を実施した。評価は、温度上昇による膨張をベローズが吸収して、溶接部に損傷を与えず、圧力を安定させ続けられるかという点と油中への酸素、窒素飽和濃度の改善という点で行い、現行のゴム製隔膜のものと比べることにした。
まず2つのコンサベータに、高温、冷却の負荷を何度も繰り返したところ、ゴム製隔膜に小さな亀裂が見え始めたが、入江工研製の金属ベローズを用いた方は、安定した動作を続けた。また、油中への酸素、窒素飽和濃度について調査したところ大幅な改善が見られ、油の耐久性向上についても実証された。
この結果を受け、B社は入江工研の採用を決定。過酷な環境下で使用するためのモデルとして、このコンサベータを組み合わせて納入したところ、電源装置を屋外に設置する事業者から高評価を得た。
また、劣化の心配がなくなっただけでなく、メンテナンスの頻度や、工数も大幅に抑えることができ、トータルで10%以上のコストダウンも手に入れることができた。