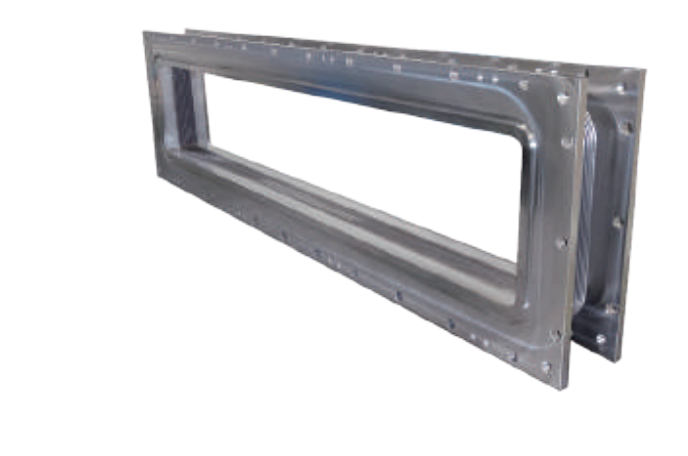
課題
グループ会社の部品が使えない!新規導入の装置に厳しいコストダウン要求が・・・
半導体・FPD製造装置メーカーD社に得意先からタブレット向けのFPD製造装置システムの追加商談が入った。しかし今回の案件は、製造工場のスペースの関係から従来のバッチ式ではなく、枚葉式のラインで製造されることから、チャンバーとバルブ、チャンバー同士をそれぞれつなぐ枚葉式専用の矩形ベローズの手配を急ぐことにした。
ところが、ここで問題が発生した。今回のシステムは、前回納品分よりコストダウンを要求されていて、単なる値引きだけでは対応が難しく、部品原価まで見直す必要が出てきたのだ。今までD社はグループ会社製のベローズを使用していたが、どんなにがんばっても今以上のコスト圧縮は見込めないため、外注品を使うという厳しい選択をせざるを得なかった。しかし、今まで外注品のベローズは取り扱ったことがなかったため、すぐに最適なものを見つけることはできなかった。
採用予定のベローズは30%が不合格?おまけに同業社で問題を起こしていた・・・
さらにコスト試算を続けた結果、国内製ベローズではどうしても合わないことがわかり、海外製を採用することも視野に入れなければならなくなった。今までベローズやバルブなど、主要な部材は品質面を考え国産にこだわってきたが、海外製の低価格な製造装置や部材が台頭しはじめ、一方では今回のようなコストダウンの要求も日に日に厳しくなっている現状もあったからだ。
早速、試作用に数セット取り寄せて、品質を確認するための実装テストを行うことにした。
ところが予想は的中した。10個中3個に溶接不良による大気漏れなどの問題が見つかったのだ。また、過去にこの製品を使った同業社製のソーラーパネル製造装置が、真空工程でリークを起こし2日間に渡って客先の生産ラインを止めたと聞きつけ、この海外製部材の採用は見送ることにした。
しかし、これでベローズの選定が振り出しに戻ってしまい、よりいっそう厳しい納期の中で、対応に追われることとなった。
課題のポイント
原価の関係から、採用経験がない外注製のベローズを使わなければならなくなった
採用を予定していた海外製のベローズには問題が山積していた
厳しい納期の中で、ベローズ探しが振り出しに戻ってしまった
解決のポイント
従来品の35%コストダウンを実現した矩形ベローズを見つけだした
国内製で特に気密溶接には定評がある金属加工メーカー製で、社内テストも全てクリア
希望納期にも柔軟に対応してくれたため、予定通り納品を完了
性能、品質はそのままで、「余分」だけを取り除いた究極の矩形ベローズが完成
解決策がなかなか見出せない担当チームは、半導体製造装置を製造している部署に相談してみた。すると「ベローズとバルブを一緒に製作している、国内唯一のメーカーの入江工研に相談してみては」と、営業担当を紹介してくれた。早速この担当者に相談したところ、「新製品の、廉価版の矩形ベローズを一度評価して欲しい」という申し入れが返ってきた。
営業担当によるとこの新製品は、バルブとチャンバーを知り尽くした入江工研が、従来の矩形ベローズに比べて誤差吸収の柔軟性と解析結果から得られた強度を維持しつつ、さらに金属材料にもこだわり、徹底的な最適化と装置機器との適合性を重視した設計を施した。その結果、重量とコストを共に35%ダウンすることができたのであった。
実装テストを行ったところ、装着したチャンバーとバルブの10箇所全てにおいて、取り付け誤差をうまく吸収し、作動中のリークや振動によるズレも見られなかった。また、検査機器を使った詳細なテストでも、全て合格値となった。廉価版でありながら定評のある溶接技術で十分な耐久性が確認できた。
一方、課題であったコストダウンについても、ベローズ単体のコストが35%も削減されたことで、配管ユニット全体のコストダウンを実現。そのことを購買部門にアピールできたことで、滞りなく購入の承諾を得ることができ、希望納期までにシステムを納めることができた。
この矩形ベローズは、性能はそのままにお客様の仕様に合わせて口径サイズを自由にカスタマイズできることから、大型FPDや有機ELなどの製造装置にも柔軟に対応でき、コストの優位性もあることからD社では標準品として継続採用することが決まった。