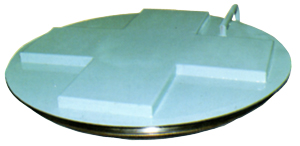
Issue.
Considering alternative solutions to improvement requests from clients. Can you find a solution...
Company B manufactures electrical power equipment. The company had a wealth of experience in transformers and transformers used in factories and commercial facilities.
One day, one of Company B's customer-users made an enquiry about a conservator built into a transformer. Specifically, the user asked the company to consider improving the deterioration of the rubber diaphragm used in the conservator.
Company B had manufactured conservators controlled by rubber diaphragms, which have a simple structure and are inexpensive, and had incorporated them into power equipment and delivered them. However, in the case of large models used outdoors or in places with extreme temperature differences, the rubber diaphragm is easily damaged, accelerating the progression of deterioration.
In addition to this, there were other requests, such as whether the frequency of maintenance of the rubber membrane could be reduced, and whether the oxygen and nitrogen saturation concentration in the oil could be reduced, so the development team at Company B decided to urgently consider alternatives to the rubber membrane.
Two solutions were narrowed down. However, neither could be realised...
After much discussion, the team decided to use metal diaphragms instead of rubber diaphragms, but they could not immediately reach a conclusion on whether they should continue to manufacture them in-house or have them produced by an external component manufacturer, as they had no experience in either case.
For the time being, they decided to make a prototype of a conservator using metal diaphragms in-house. However, the prototype was halted once and for all because many problems such as the movement of the metal being handled for the first time, structural design to cope with temperature changes, and welding techniques using special materials all came into play at once.
As the limits of in-house production became apparent, the company switched its countermeasures to the search for new component manufacturers. However, when the search began, none of the companies they had dealt with so far were able to cope, and the staff were left scratching their heads as there was little information on companies that could manufacture airtight parts.
Key points of the issue
A customer requested improvements to the rubber diaphragm used in conventional conservators.
Attempts were made to manufacture the parts in-house using metal diaphragms, but the design and welding did not go well and the attempts were abandoned.
We searched for a manufacturer capable of manufacturing airtight parts, but could not find any due to a lack of information.
Solution
Specialists in expansion and contraction design and metal welding designed and manufactured an original diaphragm using metal bellows.
Delivery of products made at a specialised factory in Japan, from material selection to assembly.
Maintenance man-hours are significantly reduced and costs are cut by 10%.
Conservators manufactured in Japan by specialists, also realising cost reductions!
Company B's development staff were at a loss as they could not find a potential manufacturer. At that time, a sales person with whom they had business in the field of power receiving and transforming equipment introduced them to a person in charge, saying that IRIE KOKEN was good at airtight welding and that they could discuss everything from material selection with them.
The IRIE KOKEN Labs representative immediately visited Company B and interviewed the company about its problems. The representative explained IRIE KOKEN's strengths, such as the high accuracy of airtight welding and the ability to freely select bellows materials and wall thicknesses according to the operating environment, as well as the fact that all these manufacturing processes are carried out at the company's own plant in Japan. In line with the proposal, we also decided to make a prototype of the optimum metal diaphragm for Company B's conservator.
The prototype was completed in about three weeks, and verification was carried out in Company B's test environment. The evaluation was made in terms of whether the bellows could absorb the expansion caused by temperature rise and keep the pressure stable without damaging the welds, and in terms of improving the oxygen and nitrogen saturation concentration in the oil, and compared with the current rubber diaphragm.
First, when the two conservators were repeatedly subjected to high temperature and cooling loads, small cracks began to appear in the rubber membrane, but the one with the metal bellows manufactured by IRIE KOKEN continued to operate stably. In addition, when the oxygen and nitrogen saturation concentrations in the oil were investigated, a significant improvement was observed, demonstrating the improved durability of the oil.
Based on these results, Company B decided to adopt IRIE KOKEN. The conservator was delivered in combination with a model for use in harsh environments, and received high praise from operators who install their power supply equipment outdoors.
In addition to eliminating concerns about deterioration, the frequency of maintenance and man-hours could also be significantly reduced, resulting in a total cost reduction of more than 10%.