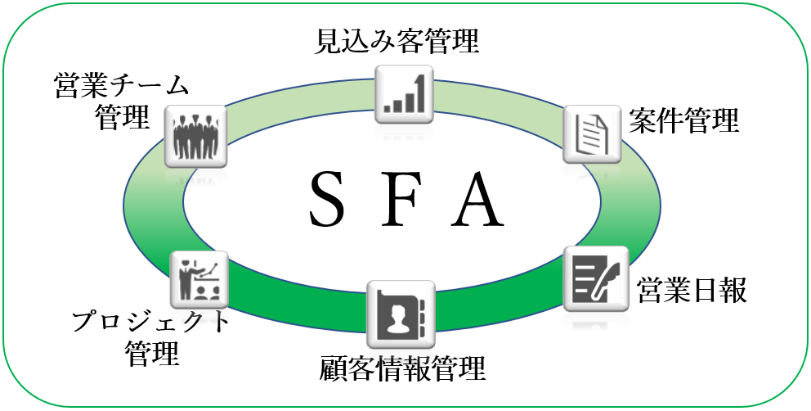
The manufacturing environment has changed significantly in recent years. Many domestic and foreign manufacturers have entered the market, and competition in terms of price and delivery time is becoming increasingly fierce. In order to adapt to this situation, our company is also implementing various measures and promoting improvement activities.
As part of our ISO 9001 quality activities, we carry out customer satisfaction surveys, and we have carried out an analysis with a special focus on QCD (quality, price and delivery).
Changes in order factors over the last five years

Trends in lost order factors over the last five years

The trend over the past five years has been that the order factors are product strength > price > delivery time, and the order factors for lost orders are price > delivery time > product strength, in that order.
The analysis shows that product competence is improving, but the price situation depends on the project and further improvement is needed in terms of delivery times.
The main reason for the improvement in product competitiveness is the use of a sales support system (SFA) to promptly share information on customer requests with the factories. Our SFA system was introduced in 2012, and now we only use this system to consolidate project information and communicate with factories on the same day from the enquiry stage, which allows us to have more time to consider the required specifications than before.
The SFA data is also used to analyse customer situations and projects, and is effective as a source of information for identifying issues and making improvements.
Delivery times, on the other hand, continue to require improvement. For this reason, we have introduced the Theory of Constraints (TOC) to improve our production capacity.
TOC is a method developed by Dr Eliyahu Goldratt in the USA, which was introduced in Japan in a book called The Goal and became a hot topic. The Goal’ became a boom for a while and many companies tried to introduce it, but many gave up because of the difficulty of the theory and the fact that it did not fit the Japanese culture.
The company was the first small to medium-sized enterprise to introduce TOC theory, arranged in a Japanese style, to the Zhongshan factory and has succeeded in increasing production capacity without increasing equipment or manpower. This management has enabled us to synchronise the production speed of bottleneck processes with the timing of production start-up, reducing stagnation time in the production process and shortening lead times. We are currently trying to continue to improve this further and work on it company-wide.
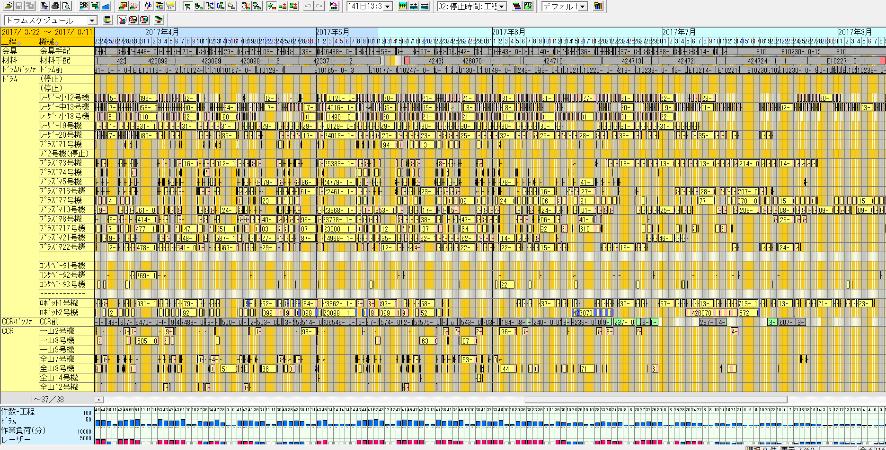
We will strive to improve QCD by adapting these systems and theories to our own needs and applying them to our sales and factories to the maximum extent possible. We will continue to promote activities to improve customer satisfaction.
As part of our ISO 9001 quality activities, we carry out customer satisfaction surveys, and we have carried out an analysis with a special focus on QCD (quality, price and delivery).
Changes in order factors over the last five years

Trends in lost order factors over the last five years

The trend over the past five years has been that the order factors are product strength > price > delivery time, and the order factors for lost orders are price > delivery time > product strength, in that order.
The analysis shows that product competence is improving, but the price situation depends on the project and further improvement is needed in terms of delivery times.
The main reason for the improvement in product competitiveness is the use of a sales support system (SFA) to promptly share information on customer requests with the factories. Our SFA system was introduced in 2012, and now we only use this system to consolidate project information and communicate with factories on the same day from the enquiry stage, which allows us to have more time to consider the required specifications than before.
The SFA data is also used to analyse customer situations and projects, and is effective as a source of information for identifying issues and making improvements.
Delivery times, on the other hand, continue to require improvement. For this reason, we have introduced the Theory of Constraints (TOC) to improve our production capacity.
TOC is a method developed by Dr Eliyahu Goldratt in the USA, which was introduced in Japan in a book called The Goal and became a hot topic. The Goal’ became a boom for a while and many companies tried to introduce it, but many gave up because of the difficulty of the theory and the fact that it did not fit the Japanese culture.
The company was the first small to medium-sized enterprise to introduce TOC theory, arranged in a Japanese style, to the Zhongshan factory and has succeeded in increasing production capacity without increasing equipment or manpower. This management has enabled us to synchronise the production speed of bottleneck processes with the timing of production start-up, reducing stagnation time in the production process and shortening lead times. We are currently trying to continue to improve this further and work on it company-wide.
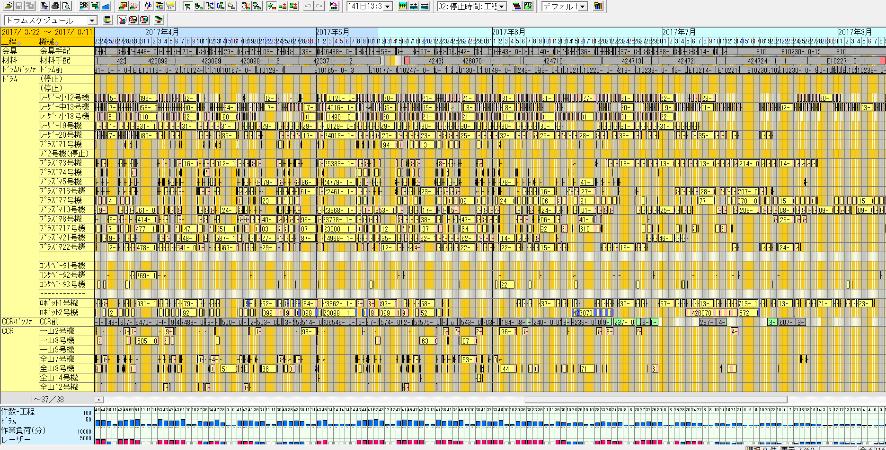
We will strive to improve QCD by adapting these systems and theories to our own needs and applying them to our sales and factories to the maximum extent possible. We will continue to promote activities to improve customer satisfaction.
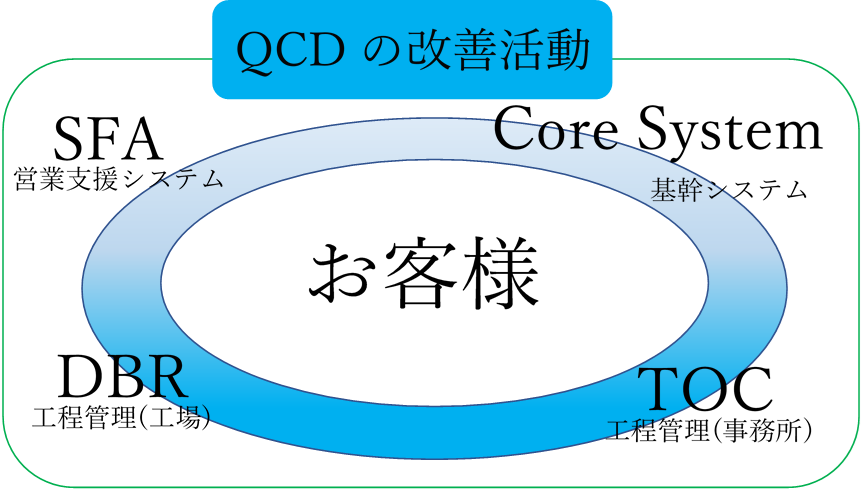