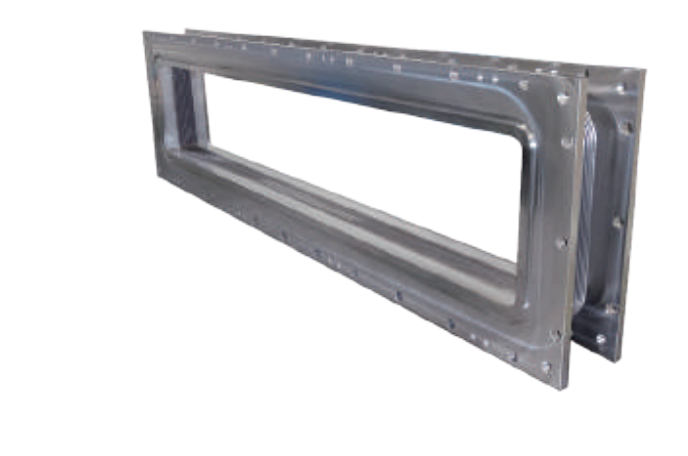
Issue
Parts from group companies are not available! Severe cost-cutting demands on newly introduced equipment...
Company D, a manufacturer of semiconductor and FPD manufacturing equipment, received an additional order from a client for an FPD manufacturing equipment system for tablets. However, due to space constraints in the manufacturing plant, this project was to be manufactured on a single-wafer line instead of the conventional batch system, so the company decided to hurry up and arrange for rectangular bellows specially designed for single-wafer systems, which connect chambers, valves and chambers respectively.
However, a problem arose here. The new system required a cost reduction compared to the previous delivery, which was difficult to meet with a mere discount, and it became necessary to review the cost of the components as well. Up until now, Company D had been using bellows made by a Group company, but no matter how hard they tried, they could not expect any further cost reduction, so they had to make the tough choice of using outsourced products. However, as they had never dealt with outsourced bellows before, they could not immediately find the most suitable ones.
30% of the bellows to be employed were rejected? On top of that, they were causing problems in the same industry ...
After further cost estimations, it became clear that the bellows made in Japan were just not suitable, and the company had to consider adopting bellows made overseas. Until now, we had stuck to domestically produced bellows, valves and other key components for quality reasons, but low-cost manufacturing equipment and components made overseas were beginning to emerge, while the demand for cost reductions such as this one was becoming more stringent by the day.
We immediately ordered several sets for prototyping and decided to conduct mounting tests to check the quality.
However, the results were predictably disappointing: problems such as atmospheric leakage due to defective welding were found in three out of 10 units. In addition, we decided not to use this foreign-made component after hearing that a solar panel production unit manufactured by a competitor using this product in the past had developed a leak in the vacuum process, stopping the customer's production line for two days.
However, this put the bellows selection back at square one, and they were forced to respond under even tighter deadlines.
Key points of the challenge
Due to cost considerations, they had to use outsourced bellows, which they had no experience in using.
The foreign-made bellows we were planning to use were riddled with problems.
The search for bellows had to go back to the drawing board due to tight deadlines.
Solution point
We found a rectangular bellows that achieved a 35% cost reduction on conventional products.
Made in Japan by a metalworking manufacturer with a particularly good reputation for airtight welding, and passed all in-house tests
Flexible response to the desired delivery date, so delivery was completed on schedule.
The ultimate rectangular bellows was completed, with only the ‘extras’ removed, while maintaining the same performance and quality
Unable to find a solution, the team in charge consulted the department that manufactures semiconductor production equipment. They were introduced to a sales representative who suggested that they consult IRIE KOKEN, the only manufacturer in Japan that manufactures bellows and valves together. The team immediately consulted this person and received an offer to ‘evaluate our new, low-cost version of rectangular bellows’.
IRIE KOKEN, which knows valves and chambers inside out, designed this new product with an emphasis on thorough optimisation and compatibility with equipment and devices, while maintaining the flexibility to absorb errors and the strength obtained from analysis results compared with conventional rectangular bellows, and also paying attention to the metal material. As a result, a 35% reduction in both weight and cost was achieved.
Mounting tests showed that in all ten of the fitted chambers and valves, mounting errors were successfully absorbed, with no leaks during operation and no misalignment due to vibration. In addition, detailed tests using inspection equipment also showed that all the values were acceptable. Despite being a low-cost version, sufficient durability was verified by the well-proven welding technology.
At the same time, the cost of the piping unit as a whole was reduced, as the cost of the bellows alone was reduced by 35%, which was also a challenge. The fact that we were able to appeal this to the purchasing department enabled us to obtain approval for the purchase without delay and to deliver the system by the desired delivery date.
The rectangular bellows can be customised freely in bore size according to the customer's specifications while maintaining the same performance, so it can be flexibly adapted to manufacturing equipment for large FPDs and OLEDs, and because of its cost advantage, Company D has decided to continue using it as a standard product.