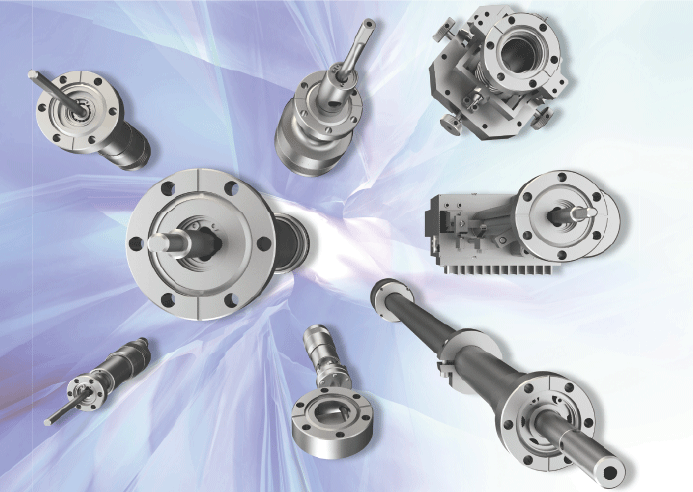
Problem
My own introduction machine can't cope with the experiment ...
A researcher at University D wanted to perform an experiment in a vacuum for his next published paper. However, as the positioning in vacuum was very important in this experiment, the problem arose that the home-made linear induction machine assembled from off-the-shelf products that they were currently using could not cope with the experiment.
After much thought, the researcher decided to install a photoelectric sensor at the tip of the linear induction machine to further improve the positioning accuracy. The idea was to install a photoelectric sensor at the tip of the linear induction machine, run a coaxial cable to the sensor and attach a flange. However, due to problems with the wiring process (length [deflection] and hardness of the coaxial cable) in the vacuum (inside the chamber), the strokes did not go well... In addition, because it was a combination of existing products, settings and adjustments were difficult and the experiment did not go smoothly.
Inadequate support system, common with machines imported from overseas...
The researcher decided to contact the manufacturer of this installation machine to see if there was a way to solve the wiring process and other problems. However, as this installation machine was made overseas, there was no customer centre in Japan and the only way to discuss or inquire about the product was through the sales agent. In addition, there was no place to consult about other off-the-shelf products customised for the introduced machine, as the place of purchase was different for each of these products.
For the time being, the researcher told the distributor that he wanted a proposal for a suitable wiring treatment method and decided to wait for a response from the manufacturer of the installed machine.
However, a week passed and no contact was made...
Key points of the problem
Photoelectric sensors were installed to improve positioning accuracy, but the wiring process in the vacuum did not work.
The installation machine was customised by assembling existing products (flanges, nipples, etc.), which made it difficult to set up and adjust.
Response to product enquiries was slow as the installed machine was manufactured overseas.
Solution points
IRIE KOKEN's custom-built hollow linear motion insertion machine solved the wiring processing problem and enabled high-precision positioning.
The machine uses mostly self-developed components and was customised to our requirements, so there was no need to spend time on installation and adjustment during testing.
IRIE KOKEN has a factory in Japan and a solid support system, so consultation and troubleshooting are quicker.
IRIE KOKEN's precise consulting skills solved the problems of the imported machine
The troubled researcher decided to search the Internet for a company that deals with installed machinery in Japan. On IRIE KOKEN's website, he found a bellows-type straight-through feed machine. Although he had known the company for some time, he had a strong image of it as a manufacturer of 'bellows' and 'valves' and did not know that it dealt in installation machines.
I immediately made an appointment and told the salesman what I wanted the machine to do and asked him to look at the actual machine, which he had designed himself. Looking into the chamber from the port, he said: 'As I thought, this type of wiring affects the operability and there is a possibility of problems occurring in the vacuum. I'm also concerned about the number of components. As soon as we take it back and discuss it with our engineers, we will give you the most suitable proposal', was the ideal response from the salesman in charge.
A few days later, a specification sheet arrived from IRIE KOKEN with a detailed design drawing. The specification was not for a straight induction machine, but for a customised assembly of a hollow straight induction machine. The hollow straight induction machine had a simple shape, with a hollow shaft through which the cables were threaded. This specification reduced the occurrence of problems around the cables, thus eliminating the problem of treating the cables in the vacuum. In addition, the bellows and most of the parts used in this installation machine were developed in-house by IRIE KOKEN, and the quality of each part was high and satisfactory.
After seeing the specifications that met the requirements of this researcher, University D decided to purchase the machine.
In fact, when they used the introduced machine that was delivered, they found that the design had been calculated for operability, which increased their work efficiency and allowed them to complete their experiments smoothly. In addition, unlike machines made overseas, IRIE KOKEN has two factories in Japan and a solid support system, which made it easy to consult with the company.