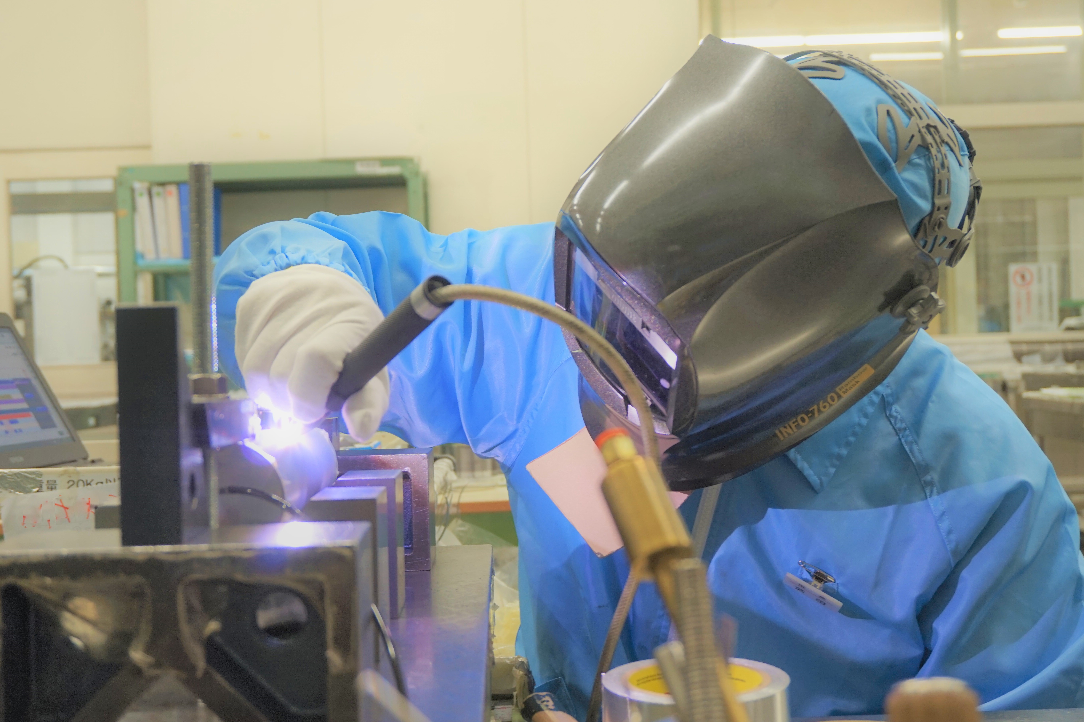
Background
Company C was experiencing problems with its water-cooled jacketed vacuum chamber.
The water-cooled jacketed vacuum chamber was not dimensionally accurate as expected and the cooling water was not flowing evenly, overheating some parts, reducing the corrosion resistance of the vacuum chamber material and causing water leakage from the water-cooling section during use...
Problem
Corrosion occurred at welds where water did not flow evenly in the water cooling section, causing water leakage.
Company C's vacuum chambers are heated to several hundred degrees Celsius for clean processing of semiconductor components and LCD panels.
However, it is known that repeated heating to several hundred degrees Celsius and cooling to atmospheric temperatures causes the stainless steel material used for the vacuum chamber to become sensitised, i.e. its corrosion resistance deteriorates. A water-cooling jacket is therefore installed around the vacuum chamber to prevent material degradation, but when the water is allowed to flow, it is found that it does not flow evenly, resulting in pools of water and partial overheating.
It was also found that welding the water-cooling jacket to the vacuum chamber required many welds, which caused distortion, reduced the strength of the material and made it impossible to produce the dimensions to the drawings.
Company C therefore consulted a machining company that makes vacuum chambers. They refused, saying that if the dimensional accuracy was 10 µm, they would have to machine it, but they could not handle a water-cooled jacket with a complex structure because it required welding technology.
Problem areas
Water leakage due to partial puddling (poor flow) in the water-cooled section and corrosion in the welds.
Dimensional accuracy of 10µm could not be achieved.
Solution
IRIE KOKEN has expertise in manufacturing water-cooled jackets, and by proposing an optimum water channel, the stagnation areas were eliminated.
Tolerances of 10 µm were achieved by design and precision machining, taking into account welding distortion.
10 µm precision was achieved through welding technology, machining and a variety of other know-how.
When we consulted IRIE KOKEN's sales staff, who happened to be visiting our company, they told us: 'IRIE KOKEN can meet any requirement. There are surprisingly few companies that can weld and machine at the same time. Welding causes distortion and thermal stress. The result is distortion and dimensional changes compared to before welding, so precision machining is essential to achieve accuracy. It is also necessary to relieve the thermal stress. These are very encouraging words.
IRIE KOKEN's sales staff started drawing diagrams on the whiteboard. Let's say we need a part with this shape.
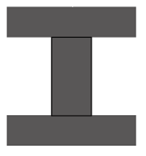
Specialist machining companies manufacture by machining. This wastes material.
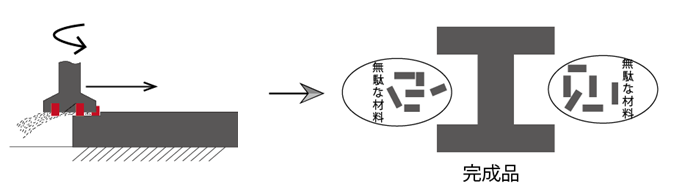
At IRIE KOKEN we weld.
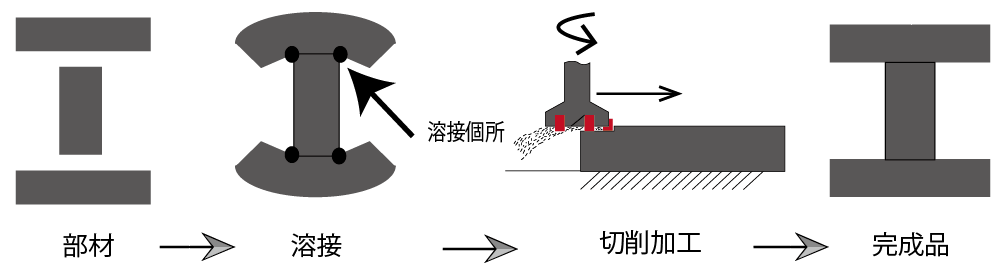
However, if welding is carried out normally, the product will be distorted in this way. By taking welding distortion into account in design and precision machining, products can be finished to an accuracy of 10 µm or less.
Smooth cooling is achieved by designing water channels in the water cooling jacket.
A simple flow of water from the inlet to the outlet of the water-cooling jacket does not ensure uniform cooling of the vacuum chamber. IRIE KOKEN has the know-how to achieve uniform cooling and has a wide range of vacuum chamber sizes available, so they were able to make the optimum proposal for Company C.
IRIE KOKEN's superior welding technology also prevents leaks that can result from poor welding. Gap corrosion in the welds of water-cooled jackets can also be predicted and avoided. I am glad we consulted IRIE KOKEN. Thanks to IRIE KOKEN's technical capabilities, we were able to build the vacuum chamber with the water-cooled jacket we wanted' (Mr K).