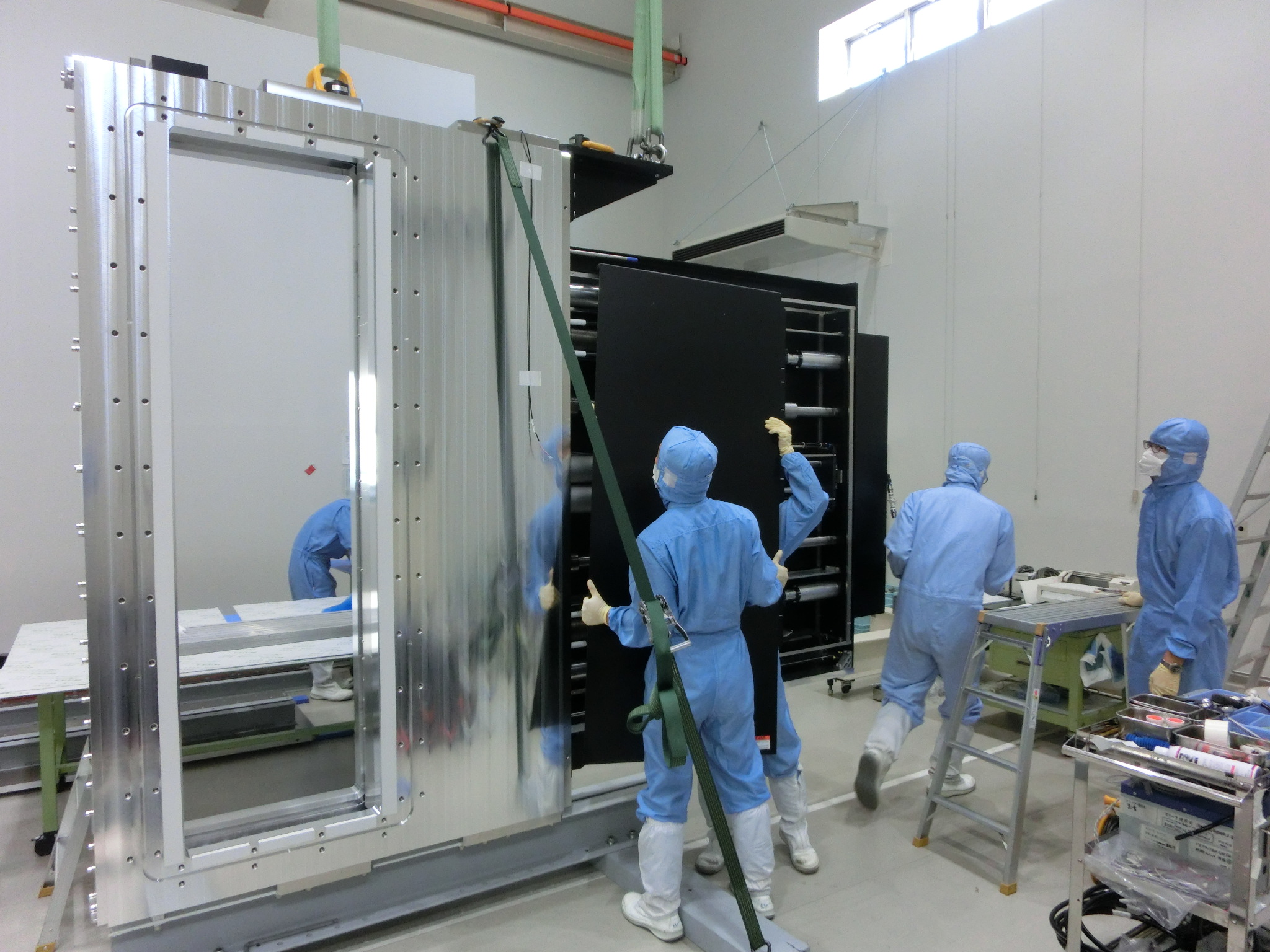
Background
Semiconductor and FPD manufacturing equipment operates 24 hours a day, and unplanned equipment downtime results directly in significant loss of profit. Therefore, in the event of equipment downtime, there is a strong need to get the equipment back up and running as quickly as possible.
Issue
Inability to get to site immediately" hinders early recovery
Mr M from the engineering department of Company G is stationed at a customer's semiconductor and FPD manufacturing facility and is responsible for managing the company's equipment. When problems occur that cause the equipment to stop, he would immediately contact the parts manufacturer to request repairs to get the equipment back up and running as quickly as possible; he would like them to go to the site immediately to check the status of the equipment failure, but in most cases this was never possible.
If we can't get them to check the situation on site, we explain the situation over the phone or try out the suggested recovery measures. However, the person on the other end of the phone is often not a technician, and sometimes it is difficult to get the message across smoothly... In the end, time is spent on the initial response and in many cases early recovery is not possible' (Mr M).
The longer unplanned equipment downtime lasted, the more it reduced productivity and was a direct cause of lost profits.
If the cause of the breakdown cannot be identified, active cooperation in restoring the equipment is not possible.
In addition, some manufacturers do not do their best to restore equipment as quickly as possible, claiming that they cannot carry out repairs until the cause of the equipment failure has been identified as being caused by their parts.
Mr M: 'There is nothing more worrying than not being able to see the specific details of the repairs and the timescale when you need to get the equipment back up and running as soon as possible.
Mr M was exhausted by the current situation where he had to negotiate with parts manufacturers to find the right time to get the equipment safely back up and running each time it was shut down.
Key points of the problem
Early restoration is not possible because the parts manufacturer is not immediately dispatched to the site, even when a repair request is made.
If the cause of the downtime is not identified, it is difficult to obtain active co-operation to restore the equipment.
Solution points
With IRIE KOKEN's CS support, they will promptly visit the site and check the status of the actual equipment.
Even if the cause of the stoppage cannot be identified, repairs can be carried out quickly to restore the equipment as soon as possible.
Technicians who are familiar with the product can quickly identify the cause of the problem and deal with it on site.
They quickly go to the site of the 'equipment stoppage' to assess the situation.
Mr M, who was concerned about recovering from an equipment failure, contacted an engineer from Irie Engineering with whom he had a long-standing relationship. He was able to find out more about IRIE KOKEN's Field Engineer service, a CS support service available to customers installing Irie Kohken gate valves.
Field Engineers," says Mr M, "are able to go to the site immediately after receiving a repair request, whether in Japan or overseas, to directly check the status of the actual equipment. This is the first step in reducing equipment downtime and minimising loss of profit due to production line stoppages.
Engineers respond to the problem so that the cause can be identified and dealt with promptly on site.
Mr M was also attracted by the fact that the people who deal with the 'field engineers' are technicians who are all familiar with the equipment and components.
It is really reassuring to know that the engineers are there from start to finish,' he says. When a technical specialist comes and checks the situation of the actual equipment, you can usually find a way to recover on the spot' (Mr M).
Even if the cause of the stoppage is unknown, repair work is carried out to restore the equipment.
However, even if technicians check the situation of the equipment on site, they may not be able to identify the cause of the stoppage. IRIE KOKEN's CS Support "Field Engineers" will not refuse repair work even if the cause is unclear, and will do their best to restore the equipment as soon as possible. In addition, spare parts are stocked at many domestic and overseas locations so that repairs can be carried out as soon as possible after the cause of the problem has been identified.
I felt that the support system shared our view that 'early restoration is our top priority' (Mr M).
Having experienced many equipment breakdowns in the past, Mr M had a strong sense of the importance of manufacturer support, including repair support, and decided to replace the valves in his own equipment with IRIE KOKEN valves.
Now, even local workers have the opportunity to receive training in maintenance and explanation of product mechanisms and functions, so that they can handle restoration to a certain extent. IRIE KOKEN's CS Support 'Field Engineers' provide daily support to manufacturing sites to improve productivity and quality, not just when problems occur.
Semiconductor and FPD manufacturing equipment operates 24 hours a day, and unplanned equipment downtime results directly in significant loss of profit. Therefore, in the event of equipment downtime, there is a strong need to get the equipment back up and running as quickly as possible.
Issue
Inability to get to site immediately" hinders early recovery
Mr M from the engineering department of Company G is stationed at a customer's semiconductor and FPD manufacturing facility and is responsible for managing the company's equipment. When problems occur that cause the equipment to stop, he would immediately contact the parts manufacturer to request repairs to get the equipment back up and running as quickly as possible; he would like them to go to the site immediately to check the status of the equipment failure, but in most cases this was never possible.
If we can't get them to check the situation on site, we explain the situation over the phone or try out the suggested recovery measures. However, the person on the other end of the phone is often not a technician, and sometimes it is difficult to get the message across smoothly... In the end, time is spent on the initial response and in many cases early recovery is not possible' (Mr M).
The longer unplanned equipment downtime lasted, the more it reduced productivity and was a direct cause of lost profits.
If the cause of the breakdown cannot be identified, active cooperation in restoring the equipment is not possible.
In addition, some manufacturers do not do their best to restore equipment as quickly as possible, claiming that they cannot carry out repairs until the cause of the equipment failure has been identified as being caused by their parts.
Mr M: 'There is nothing more worrying than not being able to see the specific details of the repairs and the timescale when you need to get the equipment back up and running as soon as possible.
Mr M was exhausted by the current situation where he had to negotiate with parts manufacturers to find the right time to get the equipment safely back up and running each time it was shut down.
Key points of the problem
Early restoration is not possible because the parts manufacturer is not immediately dispatched to the site, even when a repair request is made.
If the cause of the downtime is not identified, it is difficult to obtain active co-operation to restore the equipment.
Solution points
With IRIE KOKEN's CS support, they will promptly visit the site and check the status of the actual equipment.
Even if the cause of the stoppage cannot be identified, repairs can be carried out quickly to restore the equipment as soon as possible.
Technicians who are familiar with the product can quickly identify the cause of the problem and deal with it on site.
They quickly go to the site of the 'equipment stoppage' to assess the situation.
Mr M, who was concerned about recovering from an equipment failure, contacted an engineer from Irie Engineering with whom he had a long-standing relationship. He was able to find out more about IRIE KOKEN's Field Engineer service, a CS support service available to customers installing Irie Kohken gate valves.
Field Engineers," says Mr M, "are able to go to the site immediately after receiving a repair request, whether in Japan or overseas, to directly check the status of the actual equipment. This is the first step in reducing equipment downtime and minimising loss of profit due to production line stoppages.
Engineers respond to the problem so that the cause can be identified and dealt with promptly on site.
Mr M was also attracted by the fact that the people who deal with the 'field engineers' are technicians who are all familiar with the equipment and components.
It is really reassuring to know that the engineers are there from start to finish,' he says. When a technical specialist comes and checks the situation of the actual equipment, you can usually find a way to recover on the spot' (Mr M).
Even if the cause of the stoppage is unknown, repair work is carried out to restore the equipment.
However, even if technicians check the situation of the equipment on site, they may not be able to identify the cause of the stoppage. IRIE KOKEN's CS Support "Field Engineers" will not refuse repair work even if the cause is unclear, and will do their best to restore the equipment as soon as possible. In addition, spare parts are stocked at many domestic and overseas locations so that repairs can be carried out as soon as possible after the cause of the problem has been identified.
I felt that the support system shared our view that 'early restoration is our top priority' (Mr M).
Having experienced many equipment breakdowns in the past, Mr M had a strong sense of the importance of manufacturer support, including repair support, and decided to replace the valves in his own equipment with IRIE KOKEN valves.
Now, even local workers have the opportunity to receive training in maintenance and explanation of product mechanisms and functions, so that they can handle restoration to a certain extent. IRIE KOKEN's CS Support 'Field Engineers' provide daily support to manufacturing sites to improve productivity and quality, not just when problems occur.