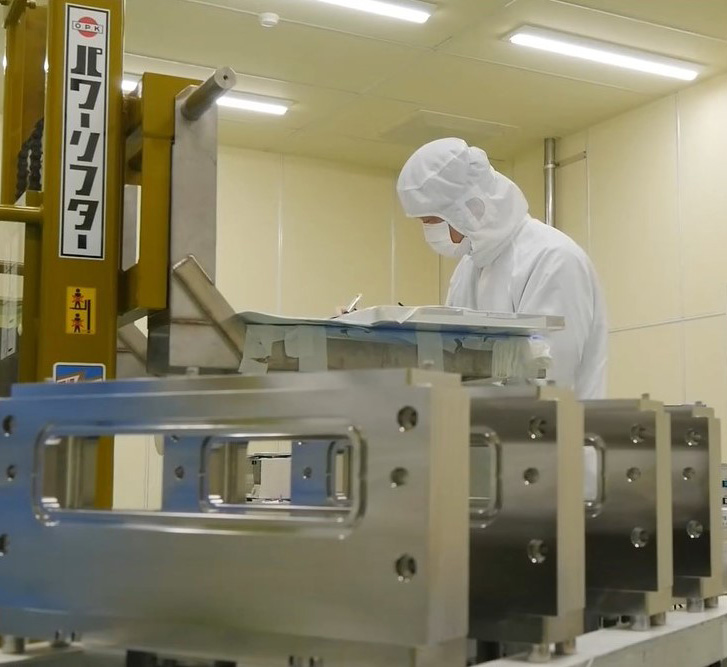
Background
Company Z decided to develop a new type of manufacturing equipment with even higher productivity than the current one in order to meet the demands of its customer device manufacturers for increased production and accelerated information gathering.
Challenges
The company wanted to improve the production performance of the equipment, but was losing time due to downtime for maintenance.
When designing the new machine, the production engineering department interviewed key suppliers and several companies about the features and specifications required for the equipment. It was found that there was a particular need for increased productivity after gate valve maintenance. However, there were some difficult issues unique to chamber systems that needed to be resolved to achieve a significant increase in productivity.
However, in order to achieve a significant increase in productivity, a difficult problem unique to the chamber system had to be solved.
When replacing the O-rings for the valve plates of the gate valves, the transfer chamber must also be brought to atmosphere when the corresponding process chamber is brought to atmosphere; after the O-ring replacement, both chambers must be brought back to vacuum, which can take up to half a day. During this time, production in the cluster itself is interrupted, resulting in reduced productivity and increased cycle time.
A further problem was that every time maintenance was carried out on one of the multiple process chambers, the cluster would stop working, resulting in a significant loss of time overall.
Mr E from the production engineering department in charge of the case began researching ways to overcome this time loss problem, but no suitable solution was found.。
The problem
The company wanted to improve the productivity of its semiconductor manufacturing equipment, but downtime during maintenance was causing a loss of time.
We gathered information but were unable to find a definitive solution.
Solution
The 'seal direction switching valve' allows maintenance to be carried out while maintaining the vacuum in the transformer chamber.
Equipment can continue to be produced during maintenance, reducing cycle time by approximately 20%.
The 'seal direction switching valve' allows valve maintenance while maintaining vacuum!
Mr E consulted the IRIE KOKEN sales representative with whom he had a long-standing relationship. He was then introduced to the company's new 'seal direction switching valve'. This valve has O-rings on both sides of the valve plate and the sealing direction can be switched between the process chamber side during normal operation and the transformer chamber side when the O-rings are changed. O-ring replacement on the process chamber side can be carried out without opening the transformer chamber side to atmosphere and while maintaining a vacuum, allowing other process chambers that are not being serviced to continue production.
The fact that the system does not have to be shut down for maintenance is a breakthrough in semiconductor production equipment. However, I was concerned that the valve standards might be different from those of conventional products, but I was reassured to hear that they were exactly the same' (Mr E, Production Engineering Department).
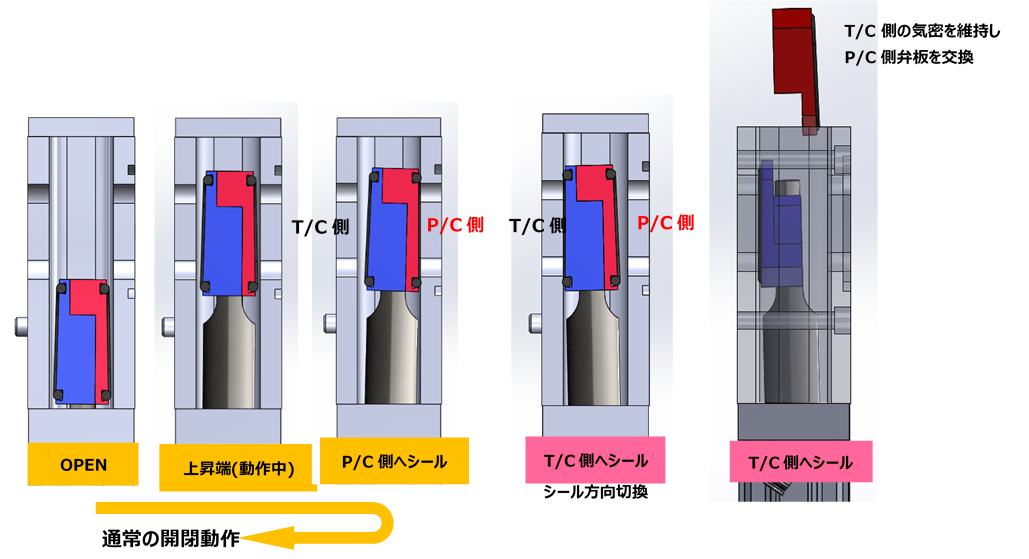
Equipment was able to continue production during maintenance, reducing cycle time by approximately 20%.
Mr E trialled and evaluated a 'seal direction switching valve' on his main production equipment. He found that while the valve was being serviced, production could continue safely in other chambers, and the exhaust time was also reduced. As a result, takt time was reduced by approximately 20% and Company Z decided to officially adopt the system. Without replacing any parts other than the valve, the company was able to significantly improve the production performance of its main product, semiconductor production equipment, and successfully meet the increased production demands of its customers.
Company Z decided to develop a new type of manufacturing equipment with even higher productivity than the current one in order to meet the demands of its customer device manufacturers for increased production and accelerated information gathering.
Challenges
The company wanted to improve the production performance of the equipment, but was losing time due to downtime for maintenance.
When designing the new machine, the production engineering department interviewed key suppliers and several companies about the features and specifications required for the equipment. It was found that there was a particular need for increased productivity after gate valve maintenance. However, there were some difficult issues unique to chamber systems that needed to be resolved to achieve a significant increase in productivity.
However, in order to achieve a significant increase in productivity, a difficult problem unique to the chamber system had to be solved.
When replacing the O-rings for the valve plates of the gate valves, the transfer chamber must also be brought to atmosphere when the corresponding process chamber is brought to atmosphere; after the O-ring replacement, both chambers must be brought back to vacuum, which can take up to half a day. During this time, production in the cluster itself is interrupted, resulting in reduced productivity and increased cycle time.
A further problem was that every time maintenance was carried out on one of the multiple process chambers, the cluster would stop working, resulting in a significant loss of time overall.
Mr E from the production engineering department in charge of the case began researching ways to overcome this time loss problem, but no suitable solution was found.。
The problem
The company wanted to improve the productivity of its semiconductor manufacturing equipment, but downtime during maintenance was causing a loss of time.
We gathered information but were unable to find a definitive solution.
Solution
The 'seal direction switching valve' allows maintenance to be carried out while maintaining the vacuum in the transformer chamber.
Equipment can continue to be produced during maintenance, reducing cycle time by approximately 20%.
The 'seal direction switching valve' allows valve maintenance while maintaining vacuum!
Mr E consulted the IRIE KOKEN sales representative with whom he had a long-standing relationship. He was then introduced to the company's new 'seal direction switching valve'. This valve has O-rings on both sides of the valve plate and the sealing direction can be switched between the process chamber side during normal operation and the transformer chamber side when the O-rings are changed. O-ring replacement on the process chamber side can be carried out without opening the transformer chamber side to atmosphere and while maintaining a vacuum, allowing other process chambers that are not being serviced to continue production.
The fact that the system does not have to be shut down for maintenance is a breakthrough in semiconductor production equipment. However, I was concerned that the valve standards might be different from those of conventional products, but I was reassured to hear that they were exactly the same' (Mr E, Production Engineering Department).
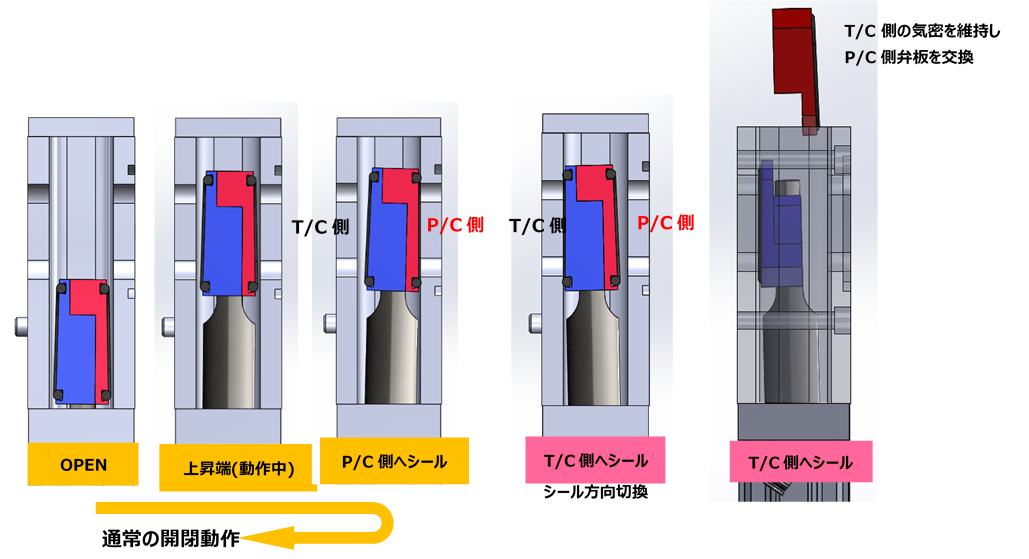
Equipment was able to continue production during maintenance, reducing cycle time by approximately 20%.
Mr E trialled and evaluated a 'seal direction switching valve' on his main production equipment. He found that while the valve was being serviced, production could continue safely in other chambers, and the exhaust time was also reduced. As a result, takt time was reduced by approximately 20% and Company Z decided to officially adopt the system. Without replacing any parts other than the valve, the company was able to significantly improve the production performance of its main product, semiconductor production equipment, and successfully meet the increased production demands of its customers.