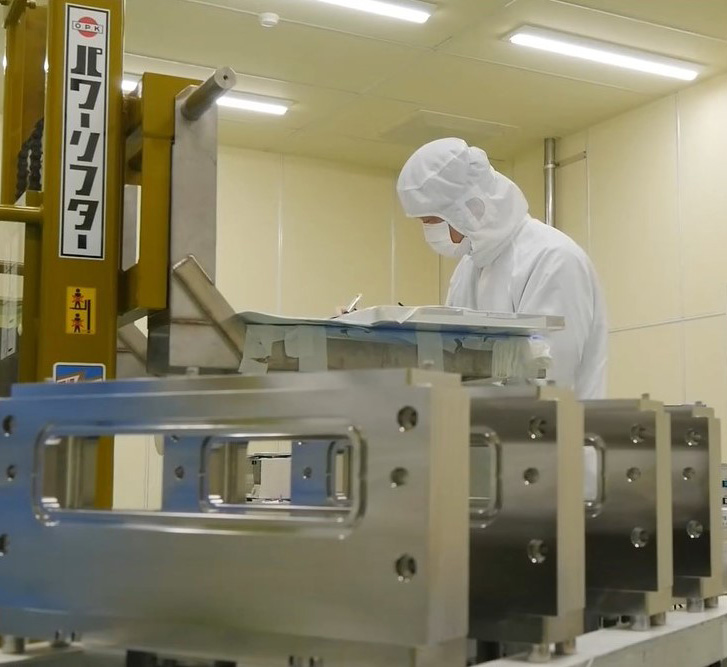
背景
Z社では、得意先のデバイスメーカーからの増産要求に応えるべく、現状よりさらに生産性が高い新型の製造装置を開発することになり、情報収集を加速していた。
課題
装置の生産性能を向上させたいが、メンテナンス時の稼働停止によりタイムロスが発生。
新型機の開発にあたり、生産技術部は主要な取引先、数社に装置に求める機能や仕様についてヒアリングを行いました。すると、ゲートバルブのメンテナンス後の生産性をもっと上げたいというニーズが特に多いことがわかりました。しかし、生産性を大幅アップするためには、チャンバーシ
ステムならではの難しい問題がありました。
ゲートバルブの弁板用Oリングを交換する際、該当するプロセスチャンバーを大気状態にすると、トランスファーチャンバーも大気状態にしなければなりません。Oリング交換終了後には両方のチャンバーを再び真空状態に戻さねばならず、それに半日ほどの時間を要することになります。その間、該当クラスターでの生産自体が中断されてしまうため、生産性は低下、タクトタイムの上昇をきたしてしまうのです。
さらに問題なのは、複数あるプロセスチャンバーそれぞれでメンテナンスを行うたびに、クラスターの稼働が止まってしまうため、全体として相当な時間のムダが発生することでした。
この件を担当する生産技術部のE氏は、このタイムロス問題をなんとかクリアできないかとリサーチを始めましたが、適切なソリューションは見つかりませんでした。
課題のポイント
半導体製造装置の生産性を向上させたいが、メンテナンス時の稼働停止がタイムロスになっている
情報収集を進めたが、決定的なソリューションを見つけ出すことができなかった
解決のポイント
「シール方向切り替え式バルブ」ならトランスチャンバーの真空を保ったままメンテナンスできる
メンテナンス時も装置の継続生産ができ、タクトタイムを約20%短縮できた
「シール方向切り替え式バルブ」なら、真空を保ったままバルブメンテナンスが可能!
E氏は、かねてから付き合いのある入江工研の営業担当に相談してみました。すると、同社の新製品の「シール方向切り替え式バルブ」を紹介されたのです。このバルブは、弁板の両側にOリングがあり、通常時はプロセスチャンバー側に、Oリング交換時はトランスチャンバー側にと、シールする方向を切り替えできるというものです。トランスチャンバー側を大気開放せず、真空を保ったままプロセスチャンバー側のOリング交換を行えるため、メンテナンスをしていない他のプロセスチャンバーは生産の継続が可能だということでした。
「メンテナンス時も稼働を停止せずに済むというのは半導体製造装置において画期的なことです。ただ、バルブの規格が従来品とは異なるのでは、と不安でしたが全く同一とのことで安心しました」(生産技術部・E氏)
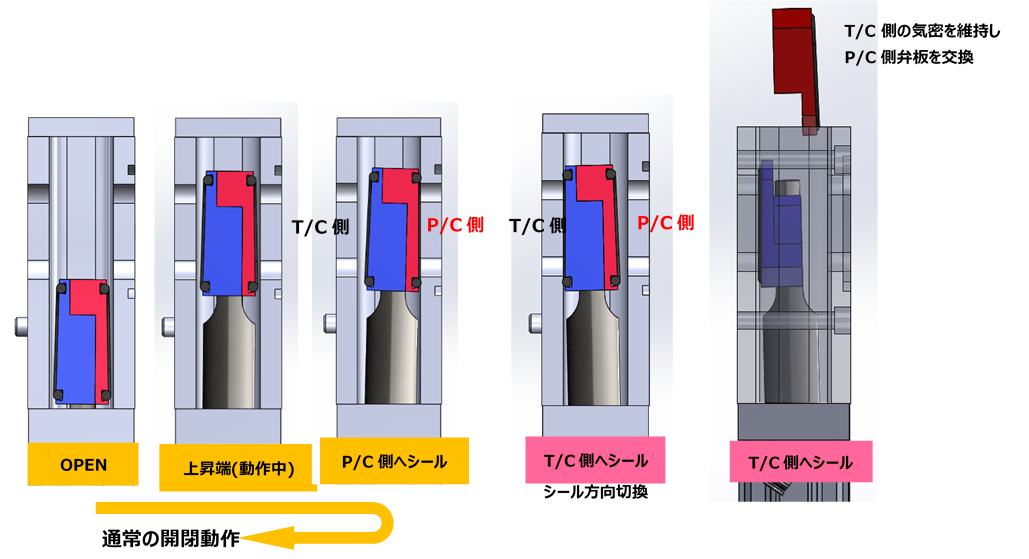
メンテナンス時も装置の継続生産ができ、タクトタイムを約20%短縮できた
E氏は、試しに主力の製造装置で「シール方向切り替え式バルブ」に切り替え、評価を行ってみました。するとバルブのメンテナンス時にも確実に他チャンバーでの継続生産ができ、排気時間も短縮できました。結果として、タクトタイムを約20%短縮することができたため、Z社では正式な採用を決定。バルブ以外の部品は取り替えることなく、社のメイン商品である半導体製造装置において生産性能の大幅な向上を果たし、得意先からの増産要求に無事対応することができました。
Z社では、得意先のデバイスメーカーからの増産要求に応えるべく、現状よりさらに生産性が高い新型の製造装置を開発することになり、情報収集を加速していた。
課題
装置の生産性能を向上させたいが、メンテナンス時の稼働停止によりタイムロスが発生。
新型機の開発にあたり、生産技術部は主要な取引先、数社に装置に求める機能や仕様についてヒアリングを行いました。すると、ゲートバルブのメンテナンス後の生産性をもっと上げたいというニーズが特に多いことがわかりました。しかし、生産性を大幅アップするためには、チャンバーシ
ステムならではの難しい問題がありました。
ゲートバルブの弁板用Oリングを交換する際、該当するプロセスチャンバーを大気状態にすると、トランスファーチャンバーも大気状態にしなければなりません。Oリング交換終了後には両方のチャンバーを再び真空状態に戻さねばならず、それに半日ほどの時間を要することになります。その間、該当クラスターでの生産自体が中断されてしまうため、生産性は低下、タクトタイムの上昇をきたしてしまうのです。
さらに問題なのは、複数あるプロセスチャンバーそれぞれでメンテナンスを行うたびに、クラスターの稼働が止まってしまうため、全体として相当な時間のムダが発生することでした。
この件を担当する生産技術部のE氏は、このタイムロス問題をなんとかクリアできないかとリサーチを始めましたが、適切なソリューションは見つかりませんでした。
課題のポイント
半導体製造装置の生産性を向上させたいが、メンテナンス時の稼働停止がタイムロスになっている
情報収集を進めたが、決定的なソリューションを見つけ出すことができなかった
解決のポイント
「シール方向切り替え式バルブ」ならトランスチャンバーの真空を保ったままメンテナンスできる
メンテナンス時も装置の継続生産ができ、タクトタイムを約20%短縮できた
「シール方向切り替え式バルブ」なら、真空を保ったままバルブメンテナンスが可能!
E氏は、かねてから付き合いのある入江工研の営業担当に相談してみました。すると、同社の新製品の「シール方向切り替え式バルブ」を紹介されたのです。このバルブは、弁板の両側にOリングがあり、通常時はプロセスチャンバー側に、Oリング交換時はトランスチャンバー側にと、シールする方向を切り替えできるというものです。トランスチャンバー側を大気開放せず、真空を保ったままプロセスチャンバー側のOリング交換を行えるため、メンテナンスをしていない他のプロセスチャンバーは生産の継続が可能だということでした。
「メンテナンス時も稼働を停止せずに済むというのは半導体製造装置において画期的なことです。ただ、バルブの規格が従来品とは異なるのでは、と不安でしたが全く同一とのことで安心しました」(生産技術部・E氏)
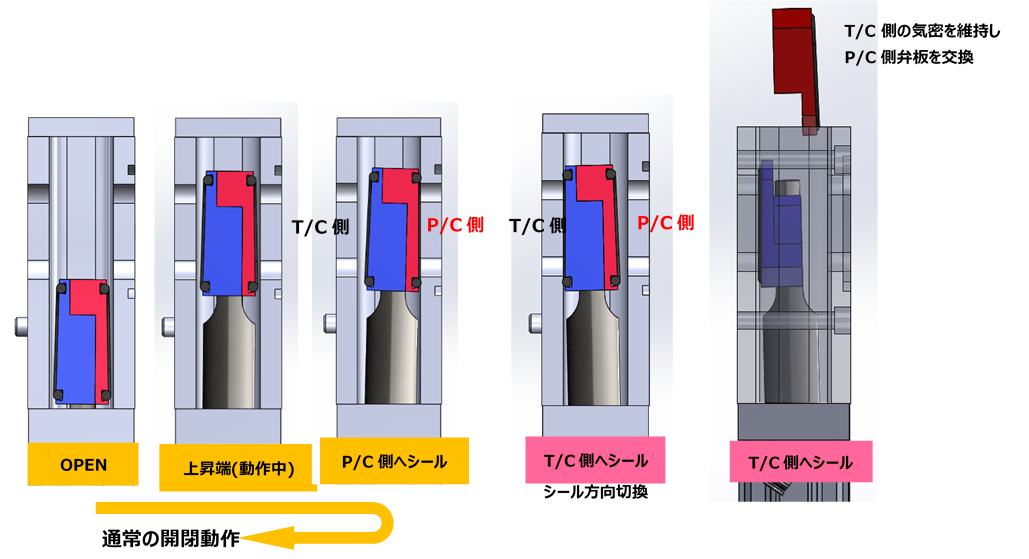
メンテナンス時も装置の継続生産ができ、タクトタイムを約20%短縮できた
E氏は、試しに主力の製造装置で「シール方向切り替え式バルブ」に切り替え、評価を行ってみました。するとバルブのメンテナンス時にも確実に他チャンバーでの継続生産ができ、排気時間も短縮できました。結果として、タクトタイムを約20%短縮することができたため、Z社では正式な採用を決定。バルブ以外の部品は取り替えることなく、社のメイン商品である半導体製造装置において生産性能の大幅な向上を果たし、得意先からの増産要求に無事対応することができました。